Technische Infos zu VSG-Glas und ESG-Glas
„Float“ Floatglas Basisglas
Zur Herstellung des derzeit am meisten verwendeten Bauglases fließt die Glasschmelze unter Schutzgas-Athmosphäre bei ca. 1.100 °C auf ein flüssiges Zinnbad. Dabei schwimmt sie wegen ihres geringeren spezifischen Gewichts auf der Zinnbad-Oberfläche. Die Glasdicke wird über die Geschwindigkeit der Rollen im Kühlbereich geregelt. Übliche Glasdicken sind 2, 3, 4, 5, 6, 8, 10, 12, 15 und 19 mm.
ESG® Einscheiben-Sicherheitsglas
Dieses thermisch vorgespannte Glas besitzt eine dreimal höhere Biegefestigkeit als Floatglas und zerfällt bei Bruch in kleine Stücke.
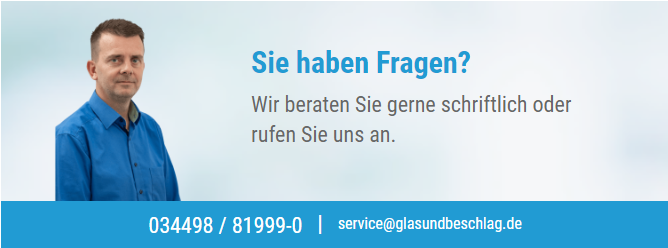
TVG® Teilvorgespanntes Glas
Dieses thermisch vorgespannte Glas wird wie Einscheiben-Sicherheitsglas (ESG®) hergestellt, weist aber nur ca. 40-50% der thermisch eingeprägten Oberflächendruckspannung auf. Diese wird durch den Kühlprozess gesteuert.
TVG® wird hauptsächlich als Verbund-Sicherheitsglas (VSG) eingesetzt, weil sein Bruchbild dem des Floatglases ähnelt. Deshalb können sich bei einem Scheiben-Bruch die einzelnen großformatigen Bruchstücke derart verzahnen, dass eine Rest-Tragfähigkeit der Scheiben gegeben ist.
Verbund-Sicherheitsglas (VSG)
VSG besteht aus mindestens 2 Glasscheiben, die mit einer elastischen reißfesten Polymerfolie so miteinander verbunden sind, dass bei einer Beschädigung der Scheibe die Bruchstücke an der Folie haften bleiben. Dies mindert das Verletzungsrisiko und gewährleistet nach dem Bruch eine Resttragfähigkeit der VSG-Einheit. Ausgangsmaterialien zur Herstellung sind Flachgläser sowie 0,38 mm dicke PVB-Folien, die auch mehrlagig laminiert werden können. Der dauerhafte Verbund zwischen Glas und Folie entsteht nach dem Schichten der einzelnen Lagen bei etwa 140°Celsius durch Walzen und anschließendes Pressen bei einem Druck von ca. 14 Bar in einem Autoklaven.
Isolierglas
Dieses Mehrscheiben-Isolierglas besteht aus einer Verglasungseinheit von mindestens zwei Gläsern, die durch einen Scheibenzwischenraum (SZR, auch Luftzwischenraum LZR genannt) von meist 8-24 mm getrennt und nur am Rand miteinander verbunden sind. Isoliergläser wirken wärme- und schalldämmend und werden auch als Sonnenschutz eingesetzt.
1. BASISGLAS
Für die Basisgläser gelten neben den in der Bauregel-Liste aufgeführten Normen die folgenden normativen Grundlagen:
DIN EN 572, Teil 1 – Basiserzeugnisse aus Kalk-Natronglas
Teil 1 – Definitionen und allgemeine physikalische und mechanische Eigenschaften
(teilweise Ersatz für DIN 1249, Teil 10)
DIN EN 572, Teil 2 – Glas im Bauwesen
Basiserzeugnisse aus Kalk-Natronglas, Teil 2 – Floatglas
(Ersatz für DIN 1249, Teil 3)
DIN EN 572, Teil 3 – Basiserzeugnisse aus Kalk-Natronglas
Teil 3 – poliertes Drahtglas
DIN EN 572, Teil 4 – Basiserzeugnisse aus Kalk-Natronglas
Teil 4 – gezogenes Flachglas (Ersatz für DIN 1249, Teil 1)
DIN EN 572, Teil 5 – Basiserzeugnisse aus Kalk-Natronglas
Teil 5 – Ornamentglas, (gemeinsam mit DIN EN 572, Teil 6 – der Ersatz für DIN 1249, Teil 4)
DIN EN 572, Teil 6 – Basiserzeugnisse aus Kalk-Natronglas
Teil 6 – Drahtornamentglas (gemeinsam mit DIN EN 572, Teil 5 – der Ersatz für DIN 1249, Teil 4)
Die Grenz-Abmaße der Nenndicken der unterschiedlichen Glasprodukte ergeben sich aus den o.g. Normen – ebenso wie die Qualitätsanforderungen und Toleranzen der optischen und sichtbaren Fehler.
Auszug aus der DIN 572, Teil 2 – Floatglas mit den Abmessungstoleranzen der Nenndicken:
|
|
2. ZUSCHNITT
Die DIN EN 572 gilt hier ergänzend.
Die generelle Längentoleranz beträgt 0,2 mm/lfm Kantenlänge.
2.1. Allgemeines
Bei Toleranz-Angaben ist in Abhängigkeit von der Glasdicke und Beschaffenheit des jeweiligen Basisglases (Sprödigkeit etc.) stets der sogenannte Schrägbruch zu berücksichtigen.
Schrägbruch
Nenndicke mm Grenzabmaße mm
3 – 6 ± 1,0
8, 10 ± 2,0
12 ± 3,0
15 ± 5,0/ – 3,0
19 ± 6,0/ – 3,0
Tabelle 2 Zulässige lineare Fehler in der Sichtfläche
Überbruch
Sollmaß
Unterbruch
Sollmaß
Die Glasabmessungen können sich bei gesäumter Kante um den doppelten Schrägbruchwert ändern. Bei nicht rechtwinkligen Elementen kann es – ähnlich dem Rückschnitt – bei den angegebenen Winkeln zu den nachstehend aufgeführten Toleranzen kommen. Dabei bleibt jedoch die Geometrie der Elemente erhalten.
2. Zuschnitt
2.1.1 Bei ESG, VSG, Isolierglas-Rückschnitt
Aus produktionstechnischen Gründen behalten wir uns das Recht auf einen Rückschnitt entsprechend der Tabelle 2b vor. Diese Maße gelten jedoch bei Wegfall des Rückschnitts als nicht zu beurteilende Zone. Unregelmäßigkeiten an der Fläche sowie an den Kanten (z. B. Überbrüche) sind kein Reklamationsgrund.
Winkel X
≤ 12,5° – 65 mm
≤ 20,0° – 33 mm
Bei einem Winkel > 20° entspricht der Rückschnitt bzw. die nicht zu
beurteilende Zone dem Abbruch.
2.1.2 Bei Floatglas – möglicher Abbruch
Winkel X
≤ 12,5° – 65 mm
≤ 20,0° – 33 mm
Tabelle 2b Rückschnitt
Bei einem Winkel > 25,0° entspricht der Rückschnitt dem Abbruch.
Die Toleranzen unter 3.1.2., Tabelle 7, dürfen nicht zu den Toleranzen in den obigen Tabellen 2a und b addiert werden,
2.2 Länge, Breite und Rechtwinkligkeit
Basierend auf den Nennmaßen für die Länge H und die Breite B muss die Scheibe in ein Rechteck passen, das um das obere Grenzabmaß vergrößert wurde und außerdem ein Rechteck umschreiben, das um das untere Grenzmaß verkleinert wurde. Dabei weisen die vorgegebenen Rechtecke einen gemeinsamen Mittelpunkt auf (s. Abb. 4) und ihre Seiten müssen parallel zueinander verlaufen.
Diese Rechtecke beschreiben gleichzeitig die Grenzen der Rechtwinkligkeit. Die Grenzabmaße für die Nennmaße der Länge H und Breite B betragen ± 5,0 mm. Die Toleranzen sind abhängig von der jeweiligen Art der Kantenbearbeitung.
2.3. Strukturverlauf bei Ornamentgläsern
Standardmäßig verläuft die Struktur möglichst parallel zum Höhenmaß. Eine gleichmäßige Ausmittelung der Struktur in der Breite (ggfs. auch Höhe) ist jedoch nicht garantiert. Abweichend kann die Struktur auch mit der Breite verlaufen, dies ist jedoch zwingend bei Bestellung anzugeben.
2.3.1 Zuschnitt SGG MASTERGLAS
2.3.2 Zuschnitt SGG SR Spiegelrohglas (Gussglas)
2.3.3 Zuschnitt SGG DECORGLAS (Gussglas)
3. BEARBEITUNG
Folgende Normen gelten ergänzend:
EN 12150 Glas im Bauwesen – Thermisch vorgespanntes Einscheiben-Sicherheitsglas
EN 1249 T 11 Glas im Bauwesen – Glaskanten
EN 1863 Glas im Bauwesen – Teilvorgespanntes Glas
3.1. Kantenbearbeitung
3.1.1 Rechtecke
3.1.1.1 Standard-Toleranzen
Kanten-Toleranzklassen nach Bearbeitungsart:
a) gesäumt
b) geschliffen/poliert
Für gesäumte Kanten gilt die Toleranz mit Schrägbruch (s. 2. Zuschnitt, Tabelle 2).
Für geschliffene/polierte Kanten gilt die folgende Tabelle:
Die Diagonaltoleranz errechnet sich aus 1,42 x Rechtecktoleranz.
Beispiel 3000 mm Kantenlänge: 1,42 x 3,0 = 4,26 mm – 4 mm Diagonaltoleranz
3.1.1.2 Sondertoleranzen
Nur gültig bei Vereinbarung vor Auftragserteilung.
3.1.2 Sonderformen
Unterteilung in die Qualitäten Standard und Sonderbearbeitung (CNC)
3.2. Bearbeitungen
Unterscheidung nach Art der Kantenbearbeitung: gesäumt, geschliffen und poliert
3.2.1 Eckabschnitt gesäumt
3.2.1.1 Standard
Toleranz ± 4 mm auf Lage/Abmaße
3.2.2 Eckausschnitt gesäumt
3.2.2.1 Standard
Toleranz ± 4 mm auf Lage/Abmaße
3.2.3 Randausschnitt gesäumt
3.2.3.1 Standard-Toleranz für Handbearbeitung – Ausschnittmaße
Tabelle 8 Randausschnitt-Toleranz HB gesäumt
3.2.3.2 Standard-Toleranz für CNC-Ausschnitt-Maße
Tabelle 9 Randausschnitt-Toleranz CNC-Bearbeitung gesäumt
3.2.4 Eckabschnitt geschliffen
3.2.4.1 Standard
Toleranz ± 2 mm (Eckabschnitt < 100 x100 mm, sonst Sonderform)
3.2.5 Eckabschnitt poliert – CNC-Bearbeitung
3.2.5.1 Standard
Toleranz ± 2 mm (Eckabschnitt < 100 x100 mm, sonst Sonderform)
3.2.6 Eckausschnitt geschliffen
3.2.6.1 Standard
Toleranz ± 2 mm (Mindestmaß bei innenliegenden Radien 15 mm!)
3.2.7 Eckausschnitt poliert – CNC-Bearbeitung
3.2.7.1 Standard
Toleranz ± 2 mm (Mindestmaß bei innenliegenden Radien 15 mm!)
3.2.8 Randausschnitt geschliffen oder poliert – CNC-Bearbeitung
Mindestmaß bei innenliegenden Radien 15 mm!
3.2.8.1 Standard-Toleranz
Toleranz ± 4 mm
Tabelle 10 Randausschnitt-Toleranz CNC-Bearbeitung geschliffen o. poliert
3.3. Lochbohrungen
3.3.1 Lochbohrungs-Durchmesser
Durchmesser
≤ 30 ± 1 mm
> 30 ± 2 mm
Lochbohrungen > 101 mm Durchmesser werden im CNC-Bearbeitungszentrum ausgeführt.
Abb. 7 Senklochtoleranz einfügen!
3.3.2 Lochbohrungsanlagen
3.4. Kantenbearbeitungsqualitäten
Grundlage der Kantenbearbeitung: DIN 1249, Teil 11
Aus produktionstechnischen Gründen können die fein geschliffenen Kanten auch poliert ausgeführt werden.
Gläser mit CNC-bearbeiteten Kanten können optisch anders wirken als mit anderen Maschinen bearbeitete Kanten.
Auf die Notwendigkeit gleicher Kantenqualität mehrerer Scheiben muss bei der Bestellung gesondert hingewiesen werden!
3.4.1 Geschnittene Kante (KG)
Diese wird auch als Schnittkante bezeichnet und ist die beim Schneiden von Flachglas entstandene unbearbeitete Kante mit scharfkantigen Rändern. Quer zu ihren Rändern sind an der Schnittkante leichte Wellenlinien (Wallnerlinien) sichtbar.
Normalerweise ist die Schnittkante glatt gebrochen, jedoch können – besonders bei dickeren Scheiben und nicht geradlinigen Formscheiben – auch unregelmäßige Bruchstellen auftreten, z. B. durch Ansatzstellen des Schneidwerkzeuges.
Außerdem können Bearbeitungsstellen (z. B. durch Brechen des Glases mit der Brechzange) zu sehen sein. Dabei sind Ausmuschelungen zulässig, wenn sie die Glasdicke der Einzelscheibe um nicht mehr als 15% verringern. Jedoch darf der maximale Radius der Ausmuschelung nicht größer als 3 mm sein.
3.4.2 Gesäumte Kante (KGS)
Diese entspricht der Schnittkante mit gebrochenen Rändern. Aus produktionstechnischen Gründen kann der Hersteller die Kanten auch schleifen oder polieren. Unzulässig dabei sind aber blanke Stellen und Ausmuschelungen.
3.4.2 Kante maßgeschliffen o. justiert (KMG – bei Ausschnitten)
Die Glasscheibe erhält ihr erforderliches Maß durch Schleifen der Kantenoberfläche. Dabei sind blanke Stellen und Ausmuschelungen zulässig.
3.4.4 Mattgeschliffene Kante (feinjustiert, KGM)
Die Kantenoberfläche erhält durch ganzflächiges Schleifen ein schleifmattes Aussehen.
Unzulässig dabei sind jedoch blanke Stellen und Ausmuschelungen.
3.4.5 Polierte Kante (KPO)
Dies ist eine geschliffene, durch Überpolieren verfeinerte Kante. Matte Stellen sind nicht zulässig, im Gegensatz zu sicht- und spürbare Polierspuren und –riefen, die zu tolerieren sind.
4. ESG® (Einscheiben-Sicherheitsglas)
Außerdem gilt die DIN EN 12150-1/-2 DIN 1249, Teil12.
Bei ESG®– Scheiben können material- und herstellungsbedingt durch Nickelsulfid-Einschlüsse Spontanbrüche auftreten. Reduziert werden kann das Restisiko solcher Brüche (s. DIN EN 14197-1, Absatz 3.2) durch die Verwendung von ESG®-H. Dabei wird das ESG-Glas über einen bestimmten Zeitraum nochmals erhitzt, wobei ein dabei eventuell auftretender Nickelsulfideinschluss in aller Regel einen Glasbruch auslöst. Jedoch garantiert auch dieser Test nicht das Aussortieren aller durch Nickelsulfid-Einschlüsse bruchgefährdeten Scheiben.
4.1 Generelle Verwerfung – gültig für ESG® aus Floatglas
Standard: 0,3 % der Mess-Strecke
Gläser mit einer Länge ≥ 5000 mm und/oder einer Höhe ≥ 2800 mm können bis zu 1,0 % der Mess-Strecke von der Geradheit abweichen (Zu prüfen ist an den Kanten und Diagonalen, kein Wert darf höher als die 0,3 bzw. 1,0 % der Mess-Strecke sein!).
Im Gegensatz zu schmalen rechteckigen Formaten kann bei quadratischen mit einem Seitenverhältnis zwischen 1:1 und 1:1,5 sowie bei geringen Glasdicken ≤ 6 mm die Abweichung von der Geradheit durch den Vorpannprozess bis zu 50 % größer sein.
Reduzieren lassen sich die genannten Werte durch Erhöhen der Glasdicke.
4.2. Örtliche Verwerfung – gültig für ESG® aus Floatglas
Standard: 0,3 mm auf 300 mm Mess-Strecke
Bei der Messung muss der Abstand zur Kante mindestens 25 mm betragen.
4.2.1 Empfohlene Mindest-Glasdicken in Abhängigkeit des Scheiben-Außenmaßes
Scheibendicke mm ESG® in mm BASISGLAS in mm
4 1000 x 2000 1410 x 2400
5 1500 x 2500 2450 x 3000
6 2100 x 3500 2500 x 4000
8 2500 x 4000 3210 x ≥ 6000
10 2800 x 5000 3210 x ≥ 6000
12 3210 x 6000 3210 x ≥ 6000
15 3210 x 6000 3210 x ≥ 6000
19 3210 x 6000 3210 x ≥ 6000
Größere Abmessungen auf Anfrage.
Die Tabelle bezieht sich nur auf die produktionstechnischen Maximalabmessungen. Die Glasdicke und die Abmessungen sind bauseits, unter evtl. Berücksichtigung einer Statik, zu bestimmen.
Tabelle 11 Minimale Glasdicke, maximales Scheibenaußenmaß
4.3. Richtlinie zur Beurteilung der visuellen Qualität für ESG®
Zur Qualität von ESG®:
Dieses thermisch vorgespannte plane Einscheiben-Sicherheitsglas im Sinne dieser Richtlinie wird folgendermaßen hergestellt:
Das Glas wird bis ca. 630-700°C aufgeheizt, dann mit anströmender Luft schnell abgekühlt. Dadurch entsteht ein „geordneter“ Spannungszustand im Glas – mit Zugspannung im Glaskern und Druckspannung an den Glasoberflächen. Dies bewirkt wiederum eine deutlich höhere mechanische und thermische Belastbarkeit im Vergleich zu normal gekühltem Glas. Außerdem bietet dieses Glas einen hohen Verletzungssschutz, denn bei Zerstörung zerbricht es in kleine stumpfkantige Krümel.
4.3.1. Geltungsbereich
Diese Richtlinie gilt für die Anwendung von thermisch vorgespanntem planem Einscheiben-Sicherheitsglas (ESG®) im Bauwesen.
Sie bildet die Grundlage zur Beurteilung der visuellen Qualität von jeweils klar in der Masse eingefärbtem Einscheiben-Sicherheitsglas aus Spiegelglas, Spiegelroh- und Gussglas. Zugrunde gelegt werden ebenfalls die folgenden Prüfungsgrundsätze, Tabellen und Angaben.
Bewertet wird die im eingebauten Zustand verbleibende lichte Glasfläche.
4.3.2 Prüfung
Maßgebend ist die Durchsicht durch die Scheibe, nicht die Aufsicht auf die Scheibe.
Die bei der Prüfung festgestellten Abweichungen werden anhand der Tabellen auf ihre Zulässigkeit geprüft.
- Fehler ≤ 0,5 mm bei Floatglas, weiß und in der Masse eingefärbt, bleiben unberücksichtigt
- Fehler ≤ 1,0 mm bei Spiegelroh- und Gussglas, weiß und in der Masse eingefärbt, bleiben ebenfalls unberücksichtigt
- die durch den Herstellungsprozess von Spiegelglas nicht immer vermeidbaren Beeinträchtigungen (z. B. Störfelder in Form von Einschlüssen dürfen mit ihrem „Hof“ nicht größer als 3 mm sein)
Geprüft wird in Anlehnung an die folgenden Normen:
DIN 1249, Ausgabe 1973 (zwischenzeitlich zurückgezogen)
Während der Prüfung befinden sich die Augen des Prüfers
- bei klarem und in der Masse eingefärbtem Floatglas in 1 m Entfernung
- bei Spiegelroh- und Gussglas – jeweils klar und in der Masse eingefärbt – in einer Entfernung von 1,5 m in Höhe der Scheibenmitte
Die Durchsicht sollte aus einem Betrachtungswinkel beurteilt werden, der der üblichen Raumnutzung entspricht. In der Regel ist das die senkrechte Betrachtungsweise. Die Lichtstärke während der Prüfung entspricht der des diffusen Tageslichts.
4.3.3 Zulässigkeit von Abweichungen
Nachfolgende Tabelle 12 enthält die Abweichungs-Möglichkeiten mit ihrer Prüfung auf Zulässigkeit.
Geltungsbereich: Ausschließlich Spiegelglas klar und in der Masse eingefärbt.
- Haarkratzer (mit dem Fingernagel nicht spürbare Oberflächenbeschädigungen
- geschlossene Blase
- kristalline Einschlüsse (unaufgeschmolzene Gemenge-Teilchen)
- Außenliegend flache Randbeschädigung bei gesäumter Kante
- leichte Ausmuschelungen bei gesäumter Kante, die die Festigkeit des Glases nicht beeinträchtigen
Tabelle für Floatglas, SG, TVG, VSG, beschichtet o. unbeschichtet
Zone Zulässigkeit pro Einheit – Spiegelglas klar und in der Masse eingefärbt
Außenliegende flache Randbeschädigungen bzw. Muscheln, die die Festigkeit des Glases
nicht beeinträchtigen und die Randverbundbreite nicht überschreiten
F Innenliegende Muscheln ohne lose Scherben, die durch Dichtungsmasse ausgefüllt sind
punkt- und flächenförmige Rückstände sowie Kratzer uneingeschränkt
Einschlüsse, Blasen, Punkte, Flecken, etc.:
Scheibenfläche ≤ 1 m2: max. 4 Stk. á ≤ 3 mm Durchmesser
Scheibenfläche > 1 m2: max. 1 Stk. á ≤ 3 mm Durchmesser je umlaufenden m Kantenlänge
Rückstände (punktförmig) im Scheibenzwischenraum (SZR):
Scheibenfläche ≤ 1 m2: max. 4 Stk. á ≤ 3 mm Durchmesser
R Scheibenfläche > 1 m2: max. 1 Stk. á ≤ 3 mm Durchmesser je umlaufenden m Kantenlänge
Rückstände (flächenförmig) im Scheibenzwischenraum (SZR):
weißlich grau bzw. transparent: max. 1 Stück ≤ 3 c m2
Kratzer: Summe der Einzellängen max. 90 mm; Einzellänge max. 30 mm
Haarkratzer: gehäuft nicht erlaubt
Einschlüsse, Blasen, Punkte, Flecken, etc.:
Scheibenfläche ≤ 1 m2: max. 2 Stk. á < 2 mm Durchmesser
1 m2 < Scheibenfläche ≤ 2 m2: max. 3 Stk. á < 2 mm Durchmesser
2 m2 < Scheibenfläche ≤ 8 m2: max. 5 Stk. á < 2 mm Durchmesser
H 8 m2 < Scheibenfläche ≤ 18 m2: max. 8 Stk. á < 2 mm Durchmesser
> 18 m2: max.10 Stk. á < 3 mm Durchmesser
Kratzer: Summe der Einzellängen max. 45 mm; Einzellänge max. 15 mm
Haarkratzer: gehäuft nicht erlaubt
max. Anzahl der Zulässigkeiten wie in Zone R
Einschlüsse, Blasen, Punkte, Flecken, etc. von 0,5 bis < 1,2 mm sind ohne
R+H Flächenbegrenzung zugelassen – jedoch keine Anhäufungen
Anhäufung = mindestens 4 Einschlüsse, Blasen, Punkte, Flecken, etc. innerhalb eines Kreisflächen-Durchmessers ≤ 20 cm
Der thermische Vorspannprozess bewirkt eine chemische und mechanische Veränderung der Oberflächenbeschaffenheit ( z. B. Pünktchenbildung, Rollenabdrücke). Die Häufigkeit und Intensität dieser Veränderungen steigt mit der Glasdicke und /oder dem Glasgewicht
F = Falzzone Glaseinstand bei Rahmenkonstruktion
R= Randzone Fläche 5% der jeweiligen lichten Breiten- und Höhenmaße
H = Hauptzone
ESG® Einscheiben-Sicherheitsglas Gussglas
F = Falzzone gilt nur für Verglasungen mit
umlaufender Rahmenkonstruktion
Für Konstruktionen und Tür-Anlagen mit freiliegenden Kanten gilt nur die Bewertung nach Zone H und R.
Die folgende Tabelle 13 zeigt Abweichungsmöglichkeiten mit Zulässigkeitsprüfung.
Geltungsbereich/Zulässigkeit pro Einheit:
nur für Spiegelroh- und Gussglas, jeweils klar und in der Masse eingefärbt
- Haarkratzer (nicht mit dem Fingernagel spürbare Oberflächenbeschädigungen)
- geschlossene Ziehblase
- kristalline Einschlüsse (unaufgeschmolzene Gemenge-Teilchen)
- aüßere flache Randbeschädigung bei gesäumter Kante
- leichte Ausmuschelungen bei gesäumter Kante ohne Beeinträchtigung der Glasfestigkeit
- geschlossene Kugelblase
ESG® Einscheiben-Sicherheitsglas Gussglas
F = Falzzone gilt nur für Verglasungen mit
umlaufender Rahmenkonstruktion
Für Konstruktionen und Tür-Anlagen mit freiliegenden Kanten gilt nur die Bewertung nach Zone H und R.
Die folgende Tabelle 13 zeigt Abweichungsmöglichkeiten mit Zulässigkeitsprüfung.
Geltungsbereich/Zulässigkeit pro Einheit:
nur für Spiegelroh- und Gussglas, jeweils klar und in der Masse eingefärbt
- Haarkratzer (nicht mit dem Fingernagel spürbare Oberflächenbeschädigungen)
- geschlossene Ziehblase
- kristalline Einschlüsse (unaufgeschmolzene Gemenge-Teilchen)
- aüßere flache Randbeschädigung bei gesäumter Kante
- leichte Ausmuschelungen bei gesäumter Kante ohne Beeinträchtigung der Glasfestigkeit
- geschlossene Kugelblase
Einheit m2
pro m2 Glasfläche zulässig |
Haarkratzer nicht spürbar zulässig auf Gesamtfläche |
Ziehblase Geschlossen L ≤ 20 mm B ≤ 1 mm L ≤ 10 mm B ≤ 1 mm Zulässig auf Gesamtfl., doch nicht in gehäufter Form |
Kugelblase Geschlosssen 3 mm – 5 mm 1 Stk/ m2
≤ 3 mm Zulässig auf Gesamtfl., doch nicht in gehäufter Form |
Einschlüsse Kristalline ≤ 3 – 5 mm |
Flache Randbeschäd. ges. Kante zulässig * |
leichte Ausmuschelung ges. Kante zulässig * |
Der spezielle Herstellungsprozess von Spiegelroh- und Gussglas bedingt kugel- oder linienförmige Einschlüsse sowie Bläschenbildung als charakteristische Gütebeschaffenheit. Strukturabweichungen durch Walzenwechsel und Musterversatz sind nicht immer auszuschließen und damit nicht reklamationsfähig.
* nicht tiefer als 15% der Scheibendicke
Tabelle 13
5. ESG®-H Einscheiben-Sicherheitsglas (ESG-Glas mit Heat-Soak-Test [HST])
ESG® wird (nach Bauregelliste A, lfd. Nr. 11.1) aus Spiegelglas hergestellt.
Durch einen anschließenden zusätzlichen Heißlagerungstest bzw. Heat-Soak-Test (H) wird aus ESG® das qualitativ höhere ESG®– H. Für dessen Herstellung gilt die Bauregelliste A, lfd. Nr. 11.4.1.
Demzufolge ist jede Scheibe ist einer Heißlagerung nach Abschnitt 2.1. zu unterziehen.
Ergänzend gelten: EN 14179 und DIN 18516-4
Bei ESG®– Scheiben können material- und herstellungsbedingt, u. a. durch Nickelsulfid (NiS)-Einschlüsse, Spontanbrüche auftreten. Reduziert werden kann das Restrisiko solcher Brüche (s. DIN EN 14197-1, Absatz 3.2) durch die Verwendung von ESG®-H. Das ESG-Glas wird über einen bestimmten Zeitraum nochmals erhitzt, wobei ein dabei eventuell auftretender Nickelsulfid-Einschluss i.d.R. einen Glasbruch auslöst. Jedoch garantiert auch dieser Test nicht das Aussortieren aller durch Nickelsulfid-Einschlüsse bruchgefährdeten Scheiben. Es bleibt ein geringes statistisches Restbruchrisiko des Glases nach Durchführung des ESG-H-Tests.
5.1 Generelle Verwerfung
Standard: 0,3 % der Mess-Strecke
Gläser mit einer Länge ≥ 5000 mm und/oder einer Höhe ≥ 2800 mm können bis zu 1,0 % der Mess-Strecke von der Geradheit abweichen (Zu prüfen ist an den Kanten und Diagonalen, kein Wert darf höher als die 0,3 bzw. 1,0 % der Mess-Strecke sein!).
Im Gegensatz zu schmalen rechteckigen Formaten kann bei quadratischen mit einem Seitenverhältnis zwischen 1:1 und 1:1,5 sowie bei geringen Glasdicken ≤ 6 mm die Abweichung von der Geradheit durch den Vorpannprozess bis zu 50 % größer sein.
Reduzieren lassen sich die genannten Werte durch Erhöhen der Glasdicke.
5.2. Örtliche Verwerfung
Standard: 0,3 mm auf 300 mm Mess-Strecke
Bei der Messung muss der Abstand zur Kante mindestens 25 mm betragen.
5.3 Spezielle Kennzeichnung
Um nachzuweisen, dass der Heißlagerungstest auch wirklich durchgeführt wurde, bekommt jede Scheibe mit thermochromer Farbe im ESG®-H-Stempel einen Punkt mit 3 mm Durchmesser. Nach dem sogenannten Heat-Soak-Test wird die Punktfarbe hellbraun. Je nach Hersteller und Zulässigkeit bei diesem durch die zertifizierende Prüfstelle ist eine Kennzeichnung des durchgeführten Heat-Soak-Tests (Heißlagerungstest) auch auf der Kante möglich (sogenannter Kantenstempel).
5.4. Der Heat-Soak-Test (Heißlagerungstest)
Dies ist ein zusätzlicher Qualitätssicherungs-Test.
Bei der Herstellung von ESG®– Scheiben können – u. a. durch Nickelsulfid-Einschlüsse, Spontanbrüche auftreten.
Ein Nickelsulfid-Einschluss kann während der Glasherstellung durch kleinste Partikel in der Glasschmelze entstehen. Dies ist auch nicht durch umfangreiche Qualitätskontrollen des Basismaterials sowie während des Herstellungsprozesses zu verhindern. Nickelsulfid-Einschlüsse sind unmittelbarer Bestandteil von Rohglas.
Deutlich reduziert werden kann das Restisiko von Spontanbrüchen aus diesem Grund jedoch durch die Verwendung von ESG®-H.
Dieses wiederum wird aus ESG®( Einscheiben-Sicherheitsglas) folgendermaßen hergestellt:
Das ESG®wird bis ca. 630 -700°C aufgeheizt, dann mit anströmender Luft schnell abgekühlt. Dadurch erhöht sich die Zugspannung im Glaskern.
Befinden sich in dieser Zugspannungszone eingeschlossene Nickelsulfid-Kristalle, dehnen sich diese durch nochmaligen Wärmeeinfluss aus – genauso wie das thermisch vorgespannte Glas. Da sich beide jedoch unterschiedlich stark ausdehnen (Grad der Ausdehnung = Ausdehnungs-Koeffizient), kann es zu einem spontanen Glasbruch (Sollbruch) kommen. Die maximale Ausdehnung der Nickelsulfid-Kristalle erfolgt zwischen 280 und 300°C.
Diese Eigenschaft wird für den Heat-Soak-Test genutzt, mit dessen Hilfe der Sollbruch noch vor Verwendung des Glases (Einbau in die Fassade) herbeigeführt werden soll. Dadurch kann Glas mit Nickelsulfid-Einschlüssen weitgehend aussortiert werden.
Funktionsweise des Heat-Soak-Tests:
Grundlage für den Heißlagerungstest, besonders für die in Deutschland verwendeten ESG®-H-Gläser, sind die EN 14179 und die BRL 2009 A, Teil 1, Anlage 11.11.
Nach dem Herstellungsprozess wird das ESG®-Glas zunächst auf Raumtemperatur abgekühlt. Danach wird die gesamte Glasmasse (Fassungsvermögen eines Heißlagerungsofens) auf mindestens 280°C aufgeheizt und dann 4 Stunden auf einer Ideal-Temperatur von 290 – 300°C gehalten. In dieser Zeit dürfen 280-320°C auch nicht kurzfristig über- oder unterschritten werden.
Für den Einsatz von ESG®-H-Gläsern innerhalb der EU kann das ESG®-Glas nach EN 14179 heiß gelagert werden.
6. TVG® Teilvorgespanntes Glas
TVG® entspricht den Anforderungen der bauaufsichtlichen Zulassung des Produzenten.
6.1 Generelle Verwerfung
Standard: 0,3 % der Mess-Strecke
Gläser mit einer Länge ≥ 5000 mm und/oder einer Höhe ≥ 2800 mm können bis zu 1,0 % der Mess-Strecke von der Geradheit abweichen (Zu prüfen ist an den Kanten und Diagonalen, kein Wert darf höher als die 0,3 bzw. 1,0 % der Mess-Strecke sein!).
Im Gegensatz zu schmalen rechteckigen Formaten kann bei quadratischen mit einem Seitenverhältnis zwischen 1:1 und 1:1,5 sowie bei geringen Glasdicken ≤ 6 mm die Abweichung von der Geradheit durch den Vorpannprozess bis zu 50 % größer sein.
Reduzieren lassen sich die genannten Werte durch Erhöhen der Glasdicke.
6.2. Örtliche Verwerfung
Standard: 0,3 mm auf 300 mm Mess-Strecke
Bei der Messung muss der Abstand zur Kante mindestens 25 mm betragen.
7. Farbe auf Glas Sieb- und Digitaldruck, Emaillierung und Lackierung
Ergänzend gelten:
DIN EN 12150 für Einscheibensicherheitsglas
DIN EN 1863 für Teilvorgespanntes Glas
DIN EN 13024-1/-2 für heißgelagertes Einscheibensicherheitsglas
EN BS 6206
7.1 Richtlinie zur Beurteilung der visuellen Qualität von emaillierten und siebbedruckten Gläsern
7.1.1 Geltungsbereich
Für voll- bzw. teilflächig farbbeschichtete Gläser, die durch Auftragen und/oder Einbrennen von organischen bzw. anorganischen Farben als Einscheibensicherheitsglas, teilvorgespanntes oder thermisch nicht vorgespanntes Glas hergestellt werden.
Für die adäquate Beurteilung der Produkte muss der Hersteller mit der Bestellung über den konkreten beabsichtigten Einsatzbereich informiert werden, besonders über folgende Details:
- Innenanwendung
- Forderungen zum HST nach TRLV-Schlusssfassung 08/2006 und Bauregelliste von bedrucktem oder emailliertem ESG®
- Einsatz für den Durchsichtbereich (Betrachtung von beiden Seiten, Berücksichtigung von Trennwänden, vorgehängten Fassaden etc.)
- Einsatz mit direkter Hinterleuchtung
- Kantenqualität und evtl. freistehende Sichtkanten (freistehende Kanten müssen geschliffen oder poliert sein!)
- Weiterverarbeitung der Monoscheiben zu THERM Isolierglas oder PROTECT® VSG (nur für freigegebene Farben)
- Referenzpunkt bei siebbedruckten Gläsern
Beim Verbinden von emaillierten, digitalbedruckten und/oder Siebdruck-Gläsern zu VSG und/oder Isolierglas wird jede Scheibe einzeln beurteilt (wie Monoscheibe).
7.1.2 Erläuterungen, Hinweise, Begriffe
7.1.2.1 Emaillierte, siebbedruckte und/oder lackierte Gläser
Durch unterschiedliche Auftragsarten ist die Glasoberfläche teilweise oder vollständig farbbeschichtet.
Dabei beeinflusst die Eigenfarbe des Glases die Farbgebung, denn die optische Beurteilung erfolgt immer durch die unbeschichtete Glasfläche auf die Farbe.
Normalerweise wird die farbbeschichtete Seite so eingebaut, dass sie von der Bewitterung (bzw. von der Nutzseite im Innenbereich) abgewandt ist.
Generell empfehlen wir eine Bemusterung des auszuführenden Glases mit der entsprechend gewünschten Farbbeschichtung vor Auftragserteilung.
Farbbeschichtete Gläser sind aufgrund einer Rest-Licht-Transmission (abhängig von Produktionsverfahren und Farbe) nicht opak.
Dabei weisen hellere Farben immer eine höhere Transmission als dunkle auf.
Optische Hell-Dunkel-Schattierungen innerhalb einer Scheibe sind bei der Betrachtung von der Rückseite dann zu sehen, wenn sich die Leuchtdichten oder die Lichtintensität (z. B. Tageslicht) auf der normalen Betrachtungsseite und der Rückseite stark unterscheiden.
Sie sind aufgrund produktionstechnischer Toleranzen der Schichtdicken nicht zu vermeiden, können aber bei der Betrachtungsmöglichkeit von beiden Seiten als störend empfunden werden.
Für die beim Einsatz der Scheiben für beidseitige Betrachtung jeweils konkreten Einsatzbedingungen bestmögliche zweckadäquate Qualität bieten die folgenden Produktionsverfahren verschiedene Lösungen
Siebdruck:
- geringste Schichtdicke
- größte Lichttransmission (farbabhängig)
- beste Farbhomogenität (Pinholes, Schattierungsnuancen und Rakelstreifen sind jedoch nicht auszuschließen)
Die Farbe wird auf einem horizontalen Siebdrucktisch mit einem Rakel durch ein engmaschiges Sieb auf die Glasoberfläche aufgedruckt. Die Dicke des Farbdicke kann jedoch nur geringfügig durch die Maschenweite des Siebes beeinflusst werden.
Die Farbschicht ist dünner als beim Walz- und Gießverfahren und deshalb – je nach gewählter Farbe – mehr oder weniger durchsichtig. Deshalb scheinen direkt auf die Hinterseite (Farbseite) aufgebrachte Medien (z. B. Dichtstoffe, Paneelklebungen, Isolierstoffe) durch.
Typisch für den Fertigungsprozess sind je nach Farbe und Anwendung leichte Streifen – sowohl in Druckrichtung als auch quer dazu – und vereinzelte leichte „Schleierstellen“, die durch punktuelles Siebreinigen in der Fertigung entstehen.
Die Lage des Druckmusters muss für das jeweilige Scheibenformat bei Bestellung vereinbart werden (0 Punkt + freier Rand). Glas- und Sieb-Toleranzen können bis zu 3 mm unbedruckte Ränder bewirken. Ein „Farbüberschlag“ auf der Glaskante ist fertigungstechnisch bedingt.
Das Bedrucken von leicht strukturierten Gläsern ist möglich, muss aber immer mit dem Hersteller abgesprochen werden.
Bei siebbedruckten Gläsern, flächig ohne Dekor kann es zu winzig kleinen unbedruckten Glasstellen kommen. Dies wird als Sternenhimmel bezeichnet.
Walzverfahren:
- mittlere Schichtdicke
- geringe Lichttransmission (farbabhängig)
- gute Farbhomogenität von außen, jedoch durch die Mikroverzahnung der Walze eine in Ziehrichtung orientierte Oberflächenstruktur (von der Rückseite her wahrnehmbar, bei Gegenlicht als feine Streifen)
Die Emaille-Farbe wird mit einer gerillten Gummiwalze auf die Glasscheibe übertragen. Weil dies umweltfreundlch ohne Zugabe von Lösungsmitteln erfolgt, wird bei absolut planer Glasoberfläche eine homogene Farbgebung gewährleistet. Dabei sind allerdings Farbdicke und Deckkraft nur bedingt einstellbar. Typisch für dieses Produktionsverfahren ist die Sichtbarkeit der gerillten Walzenstruktur auf der Farbseite.
Normalerweise sieht man diese Rillen jedoch von der Vorderseite aus durch das Glas betrachtet (s. Begriff „Betrachtungsweise unter 7.1.3) nicht. Zu beachten ist, dass ein direkt auf die Hinterseite (Farbseite) aufgebrachtes Medium (z. B. Dichtstoffe, Isolierungen, Paneelkleber) durchscheint.
Deshalb sind gewalzte Emaille-Gläser normalerweise für den Durchsichtbereich ungeeignet. Die vorgesehenen Anwendungsbereiche müssen deshalb bei der Bestellung konkret mit dem Hersteller abgestimmt werden (Erscheinung Sternenhimmel à siehe auch Siebdruck)
Ein speziell an den Längskanten (Blick in Laufrichtung der Walzen) leicht welliger „Farbüberschlag“ ist verfahrensbedingt.
Digitaldruck (Farbbedruckung digital):
- mittlere bis geringste Schichtdicke
- größte bis geringse Lichttransmission (farbabhängig)
- beste Farbhomogenität (Pinholes, Schattierungsnuancen und sichtbare Streifen in Druckrichtung sind jedoch nicht auszuschließen)
Die keramische Farbe wird auf einem Drucktisch mit Spezialdruckköpfen auf die Glasoberfläche aufgetragen. Die Farbdicke kann dabei individuell von transluzent bis opak eingestellt werden.
Typisch für den Fertigungsprozess sind leichte Streifen in Druckrichtung.
Deckungsgleiche Drucke sowie ein- oder mehrfarbige Designs und Bilder sind möglich.
Spritzlackierung (LACK):
- hohe Schichtdicke
- geringste Lichttransmission (nicht bei transluzenten Lackierungen)
- sehr gute Farbhomogenität von außen, geringe Oberflächenstrukturierung auf der Lackierseite
- Nassauftragsmengen zwischen 100 und 450g/m2
- blickdichte Lackierungen
- hohe Wiederholgenauigkeit der Farbtöne
Der Lack wird mit einem Luftdruck von 2 bis 6 Bar aus einer Spritzpistolen-Düse zerstäubt. Die Menge der Farbe, die dabei aufgetragen wird, steuert der Lackierer manuell. Das Aushärten der 2K-Farbsysteme erfolgt in einem Trockenofen, dessen festgelegter Aufheizzyklus die vollständige Lack- und Härterreaktion sicherstellt.
Alle möglichen Oberflächengeometrien inklusive Strukturgläsern können sowohl blickdicht (zum Verdecken von Dichtstoffen, Montageklebebändern oder Klebern = Uni-Farbtöne RAL/NCS S/Metallic) als auch transluzent (für Sandstrahl- und Ätzeffekte) lackiert werden.
Generell für alle Farbverarbeitungsverfahren ist eine Bemusterung vor Auftragsdurchführung zu empfehlen.
7.1.2.2 Kantenqualität
Wenn kein Farbüberschlag auf Kante und Fase (nur bei polierter Kante möglich) gewünscht ist, muss das ausdrücklich bestellt werden.
7.1.3 Prüfung von emaillierten und siebbedruckten Gläsern
Beurteilung der visuellen Qualität:
aus mindestens 3 m Entfernung
Blickwinkel von 90° zur Oberfläche
|
bei normalem Tageslicht (keine direkte Sonneneinstrahlung o. Gegenlicht, keine künstliche
Beleuchtung) Betrachtung durch die nicht emaillierte/siebbedruckte Seite; bei Gläsern für den
Durchsichtbereich von beiden Seiten
Randzone
umlaufend 15 mm
Hinter der Prüfscheibe befindet sich im Abstand von 50 cm ein lichtundurchlässiger mattgrauer Hintergund. Fehler dürfen nicht markiert sein.
Aus dieser Entferung nicht erkennbare Fehler werden nicht bewertet!
Für ESG®-spezifische Fehler gilt die visuelle Richtlinie für Einscheiben-Sicherheitsglas.
Bei der Fehler-Beurteilung wird in Falz- und Hauptzone unterschieden (s. folgende Abb.):
* Bei Bestellung von Sichtkanten erstreckt sich die Hauptzone bis zum Scheibenrand, die Randzone entfällt. Die folgenden Tabellen 14 und 15 zeigen die Anforderungen an die visuelle Qualität:
Besondere Hinweise
Hergestellt werden können Metallicfarben, Ätzcharakterfarben, rutschhemmende Beschichtungen oder mehrfarbige Drucke. Sonderwünsche müsssen mit dem Hersteller besprochen werden. Dafür gelten die folgenden Toleranzen nicht, deshalb empfehlen wir eine Bemusterung.
Abb. zu Tabelle 14: Felerarten/Toleranzen Toleranz der Abmessungen bei Teil-Emaill
für voll- o. teilfächig emaillierte Gläser (Druckgröße)
Emaill-Lagetoleranz, gemessen von Referenzkante
Besondere Hinweise
Hergestellt werdenkönnen Metallicfarben, Ätzcharakterfarben, rutschhemmende Beschichtungen oder mehrfarbige Drucke. Sonderwünsche müsssen mit dem Hersteller besprochen werden. Dafür gelten die folgenden Toleranzen nicht, deshalb empfehlen wir eine Bemusterung.
Fehlerarten/Toleranzen für für voll- o. teilfächige Emaillierungen
* Fehler ≤ 0,5 mm („Sternenhimmel“ oder „Pinholes“ = kleinste Fehlstellen im Emaill)
sind zulässig und werden generell nicht berücksichtigt. Vor dem Vorspannprozess ist die Ausbesserung mit Emaille-Farbe zulässig und danach mit organischem Lack. Dieser darf jedoch nicht verwendet werden, wenn das Glas zu Isolierglas weiterverarbeitet werden soll und sich die sich die Fehlstelle im Bereich der Randabdichtung befindet. Die ausgebesserten Fehlstellen dürfen aus 3 m Entfernung nicht sichtbar sein.
** Die Emaill-Lagetoleranz wird vom Referenzpunkt aus gemessen.
Bei Randsiebdruck sind Doppelbedruckungen nicht zu vermeiden.
Fehlerarten/Toleranzen für Sieb- und Digitaldruck sowie Lackierung
Fehlerart Hauptzone Falzzone
Tabelle 15: Felerarten/Toleranzen für siebbedruckte Gläser
Bei Randsiebdruck sind Doppelbedruckungen nicht zu vermeiden.
* ≤ 0,5 mm („Sternenhimmel“ oder „Pinholes“ = kleinste Fehlstellen im Siebdruck)
sind zulässig und werden generell nicht berücksichtigt.
** die Design-Toleranz wird vom Referenzpunkt aus gemessen
*** Fehler müssen mindestens 250 mm auseinander liegen
**** die Toleranz kann sich summieren: Fehlerart Haupt- und Falzzone, Felstellen im Siebdruck
Serienfehler (Positionen gleicher Scheiben-Abmessungen und Druck)
Tritt bei mehr als drei Scheiben je Postion der gleiche Fehler an der der gleichen Stelle auf, wird dies als Serienfehler bewertet.
Die genannten Toleranzen können irritierend wirken für:
geometrische Figuren
sogenannte Lochmasken unter 3 mm Größe
Verläufe von 0 bis 100 %
Hier ist eine 1:1-Bemusterung empfehlenswert.
Geometrie- und Abstands-Toleranzen im Zehntelmillimeter-Bereich sind grobe Abweichungen.
Diese Anwendungen müssen mit dem Hersteller ausnahmslos auf Machbarkeit überprüft werden.
Abb. 12 zu Tabelle 15: Fehlerarten/Toleranzen für siebbedruckte Gläser
Grundsätzlich gilt Tabelle 15 auch bei der Beurteilung von Druckfehlern.
Gilt sinngemäß auch für ovale und andere Geometrien (Bewertung = Breite x Höhe)
7.1.5 Beurteilung des Farbeindruckes
Unter bestimmten Licht- und Betrachtungssituationen können beim Vergleich von emaillierten Glastafeln grundsätzlich nicht auszuschließende Farbabweichungen auftreten. Diese können vom Betrachter subjektiv als störend oder nicht störend bewertet werden. Mögliche Ursachen für diese Farbunterschiede werden nachfolgend erläutert.
7.1.5.1 Art des Basisglases und Einfluss der Farbe
Das verwendete Basisglas ist in der Regel ein Floatglas (plane Oberfläche, hohe Lichtreflexion).
Zusätzlich kann dieses mit reflexionserhöhenden oder -vermindernden Beschichtungen versehen sowie leicht geprägt (z. B. Strukturglas) sein. Ein weiterer Einflussfaktor ist die Eigenfarbe des Glases, die hauptsächlich von der Dicke und der Glasart (z. B. durch- o. entfärbt) bestimmt wird.
Farbunterschied bei Nachlieferungen von farblich veredelten Gläsern – Hinweis
Verantwortlich für die Farbgebung der Emailfarbe sind die anorganischen Bestandteile, die geringen Schwankungen unterliegen. Diese Stoffe sind mit „Glasfluss“ vermengt, damit sich die Farbe im Vorspannprozess mit der Glasoberfläche „vermengt“ und untrennbar verbindet. Die endgültige Farbgebung ist erst nach diesem „Brennprozess“ zu sehen.
Bei einer Glasoberflächen-Temperatur von ca. 600 – 620 °C verbinden sich die Farben innerhalb von 2 – 4 Minuten mit dem Glas. Dieses enge „Temperaturfenster“ kann besonders bei unterschiedlichen Scheibengrößen nicht identisch eingehalten werden. Ausschlaggebend für den Farbeindruck sind außerdem die verschiedenen Farbauftragsverfahren bzw. -arten. So wird beispielsweise mit dem dickeren Farbauftrag im Walzverfahren eine höhere Deckkraft erreicht als mit dem dünneren beim Siebdruck.
7.1.5.2 Lichtart, bei der das Objekt betrachtet wird
Lichtverhältnisse verändern sich in Abhängigkeit von der Jahres- und Tageszeit und den Wetterbedingungen. Das wiederum verursacht die unterschiedliche Stärke der Licht-Spektralfarben, die durch die verschiedenen Medien (Luft, 1. Oberfläche, Glaskörper) auf die Farbe treffen. Die Farbpigmente reflektieren oder absorbieren sie – je nach Einfallswinkel und Lichtquelle, so dass die Farbe immer unterschiedlich erscheint.
Info: Das menschliche Auge reagiert unterschiedlich auf verschiedene Farben: Beispielsweise nimmt es Farbunterschiede bei Blautönen viel stärker wahr als bei Grüntönen.
7.1.5.3 Bedingungen für einen objektiven Bewertungsmaßstab
Eine objektive visuelle Einschätzung und Bewertung von Farbunterschieden ist aus den o. g. Gründen nicht möglich.
Wünscht der Kunde jedoch einen objektiven Bewertungsmaßstab für den Einbauort, ist die Verfahrensweise vorher mit dem Lieferanten abzustimmen.
Die Messung des Farbunterschiedes erfolgt unter vorher exakt definierten Bedingungen (Glasart, Farbe, Lichtart).
Der grundsätzliche Ablauf dabei ist folgendermaßen:
- Bemusterung und Auswahl einer oder mehrerer Farben
- Festlegung der Toleranzen je Farbe durch den Kunden
Beispiel:
erlaubte Farbabweichung: ∆ L* ≤ … ∆ C* ≤ … ∆ H* ≤ … im CIELAB-Farbsystem
Messbedingungen: Lichtart D 65 (Tageslicht) mit d/8° Kugel-Geometrie,
10° Normalbeobachter, Glanz eingeschlossen
- Machbarkeits-Überprüfung der Einhaltbarkeit der vorgegebenen Toleranz (Rohstoff-Verfügbarkeit, Auftragsumfang usw.) durch den Lieferanten
- Herstellung eines 1:1-Produktmusters und Freigabe durch den Kunden
- Fertigung des Auftrages innerhalb der festgelegten Toleranzen
Wird kein besonderer Bewertungsmaßstab vereinbart, gilt ∆ E* ≤ 2,90 unter den im obigen Beispiel angegebenen Messbedingungen.
7.1.6 Anwendungshinweise
- Anwendungen mit (Teil-) Emaille und (Teil-) Siebdruck zur Folie bei Verbund-Sicherheitsglas (VSG) müssen mit dem Hersteller auf Machbarkeit geprüft werden. Das gilt speziell beim Einsatz von Ätzton zur Folie, da die optische Dichte des Ätztones stark herabgesetzt werden kann und seine Dichte nur bei Verwendung auf Ebene 1 oder 4 erhalten bleibt.
- Emaillierte, sieb- und digital bedruckte Gläser mit anorganischen (keramischen) Farben können nur in der Ausführung Einscheiben-Sicherheitsglas ESG® oder Teilvorgespanntes Glas TVG® hergestellt werden. Lackierungen sind jedoch auch auf unvorgespannten Gläsern möglich.
- Nachträgliches Bearbeiten der Gläser (egal, welcher Art) ist ausnahmslos unzulässig, da es die Produkteigenschaften unter Umständen wesentlich beeinflusst.
- Beim Einsatz emaillierter Gläser als monolithische Scheibe oder in Verbindung mit Verbund-Sicherheitsglas sind die geltenden Bestimmungen, Richtlinien und Normen vom Anwender zu berücksichtigen.
- Emaillierte Gläser in der Ausführung Einscheiben-Sicherheitsglas ESG® können einem zusätzlichen Qualitätssicherungs-Prozess, dem Heat-Soak-Test (Heißlagerungstest) zu ESG-H ®, unterzogen werden. Der Anwender muss die Notwendigkeit prüfen und dem Hersteller mitteilen.
- Die Statik-Werte emaillierter Gläser sind nicht mit einem nicht bedruckten oder nicht emaillierten Glas gleichzusetzen (siehe TLRV bzw. ZiE).
7.2 Metallic-Farben
Herstellungsprozess und Pigmentierung von Metallic-Farben können Wahrnehmungsunterschiede des Farbeindruckes verursachen. Deshalb entsteht bei neben- oder übereinander eingebauten Gläsern kein gleichmäßiges homogenes Erscheinungsbild. Diese Eigenheit von Metallic-Farben bewirkt ein lebendiges Fassadenbild – auch bei unterschiedlichen Betrachtungswinkeln.
8. Verbund-Sicherheitsglas (VSG)
8.1 Maßtoleranzen
Die Toleranzen entsprechen grundsätzlich der DIN EN ISO 12543 (Norm für Gläas im Bauwesen, Verbundglas, Verbund-Sicherheitsglas). Gültig sind die entsprechenden Maßtoleranzen der eingesetzten Vorprodukte im VSG-Element und außerdem die zulässigen Versatz-Toleranzen (Tab. 16 und 17).
Beispiel:
VSG aus 6 mm ESG®/ 0,76 PVB / 6 mm TVG®; Kanten poliert
Abb. 15: Grenzmaße für rechtwinklige Scheiben
Maßtoleranz der Einzelscheibe ± 1,5 mm plus zusätzliche Versatz-Toleranz ± 2 mm ergibt eine Summe der zulässigen Versatz-Toleranz von ±3,5 mm
8.2 Verschiebe-Toleranzen
Aus fertigungstechnischen Gründen können sich die Einzelscheiben im Verbundprozess gegeneinander verschieben.
Abb. 16: Versatz
Bei VSG aus 2 oder mehreren Gläsern wird standardmäßig jede Einzelscheibe nach DIN 1249, Teil 11, bearbeitet. Zu den Verschiebe-Toleranzen addieren sich die Zuschnitt-Toleranzen.
Die längste Kante des Elementes findet in der Tabelle 16 oder 17 Anwendung. [ergänzend]
für Rechtecke gilt: für Sonderformen gilt:
Scheibe bis zulässiges Höchstmaß für den Scheibe bis zulässiges Höchstmaß für den
Versatz je VSG Nenndicke Versatz je VSG Nenndicke
8.3 Dicken-Toleranz
Das Dicken-Abmaß für VSG darf nicht größer sein als die Summe der einzelnen Glasscheiben lt. der Normen für Basisglas (EN 572).
Das Grenzmaß von Zwischenschicht < 2 mm bleibt unberücksichtigt. Für Zwischenschichten ≥ 2 mm wird ein Abmaß von ≤ 0,2 mm berücksichtigt.
Beispiel:
Verbundglas aus 2 x Floatglas mit einer Nenndicke von 3 mm und einer Zwischenschicht von 0,5 mm.
Bei Floatglas mit einer Nenndicke von 3 mm betragen die Grenzabmaße + 0,2 mm (nach EN 572-2).
Deshalb ist die Nenndicke 6,5 mm und die Grenzabmaße betragen ± 0,4 mm.
8.4 Bearbeitung
Mögliche Kantenbearbeitung der Einzelscheiben bei VSG-Elementen aus zwei oder mehreren Gläsern: nach DIN1249, Teil 11KG, KGS, KMG,KGN oder KPO. Auch die Glaskante des Gesamtpakets kann bearbeitet werden.
Bei ESG® und TVG® ist keine nachträgliche Egalisierung des Kantenversatzes möglich.
Bei kombinationen aus nicht vorgespannten Gläsern ist eine Nachbearbeitung zulässig.
8.5 Richtlinien zur visuellen Beurteilung von VSG nach DIN ISO 12543-6; 1998
8.5.1 Anwendungsbereich
Diese Norm definiert die Fehler-Toleranz in der Glasscheibe, der Zwischenschicht und beim Prüfverfahren in Bezug auf das Aussehen. Besondere Aufmerksamkeit gilt den Annahmekriterien im Sichtfeld zum Lieferzeitpunkt.
8.5.2 Normative Verweisungen
Diese Europäische Norm enthält auch Festlegungen aus anderen Publikationen, die an den jeweiligen Textstellen mit nachfolgender Nennung der Publikationen zitiert werden. Diese normativen Verweisungen können datiert oder undatiert sein. Bei datierten (starren) Verweisungen gehört die Publikation in der datierten Form zur Norm, spätere Änderungen der Publikation bedürfen der vorherigen Einarbeitung in diese Norm. Bei undatierten Verweisungen gilt die jeweils letzte Ausgabe der benannten Publikation.
DIN EN ISO 12543-1
Glas im Bauwesen – Verbundglas und Verbund-Sicherheitsglas – Teil 1:
Definition und Beschreibung von Bestandteilen
DIN EN ISO 12543-5
Glas im Bauwesen – Verbundglas und Verbund-Sicherheitsglas – Teil 5
Maße und Kantenbearbeitung:
8.5.3 Definition
Für die Anwendung dieser Norm gelten neben den Definitionen von EN ISO 12543-1 die folgenden:
- punktförmige Fehler: undurchsichtige Blasen, Flecken und Fremdkörper
- lineare Fehler: Fremdkörper, Kratzer und Schleifspuren
- andere Fehler: Glasfehler wie Kerben und Zwischenschicht-Fehler wie Schrumpfung,
Falten und Streifen
- undurchsichtige Fehler: sichtbare Fehler im verbundglas wie Zinnflecken Einschlüsse im Glas
oder in der Zwischenschicht
- Blasen: Luftblasen im Glas oder in der Zwischenschicht
- Fremdkörper: jeder während der Herstellung in das Verbundglas eingedrungene
unerwünschete Gegenstand
- Kratzer o. Schleifspuren: lineare Beschädigung der äußeren Oberfläche des Verbundglases
- Kerben: von einer Kante in das Glas verlaufende scharf zugespitzte Risse oder
Sprünge
- Falten: sichtbare Beeinträchtigungen, die bei der Herstellung durch Falten in
der Zwischenschicht entstehen
- Durch Inhomogenität der Zwischenschicht bedingte Streifen:
durch Herstellungsfehler verursachte optische Verzerrungen in der Zwischenschicht
8.5.4 Fehler in der Oberfläche
8.5.4.1 Streifen als Folge von Inhomogenität der Zwischenschicht
Bei Anwendung des unter 7.1.3 angegebenen Prüfverfahrens ist die Zulässigkeit punktförmiger Fehler ?? abhängig von der Größe und Häufigkeit des Fehlers, der Größe der Scheibe und der Scheibenanzahl des Verbundglases. Dies wird in Tabelle 18 verdeutlicht.
- Fehler < 0,5 mm sind zulässig und werden nicht berücksichtigt
- unzulässig sind Fehler > 3 mm
- die Zulässsigkeit von punktförmigen Fehlern in Verbundglas ist unabhängig von der Dicke des einzelnen Glases
- Eine Anhäufung von Fehlern ensteht, wenn vier oder mehr Fehler weniger als 200 mm voneinander entfernt liegen. Bei 3-scheibigem Verbundglas verkürzt sich dieser Abstand auf 180 mm, bei 4-scheibigem auf 150 mm und bei 5- oder mehrscheibigem auf 100 mm.
- Ist eine Zwischenschicht dicker als 2 mm, erhöht sich die Anzahl der zugelassenen Fehler in Tabelle 15 um 1.
Tab. 18: Zulässige punktförmige Fehler in der Sichtfläche
8.5.4.2 Lineare Fehler in der Sichtfläche
Bei Anwendung des unter 8.5.9 angegebenen Prüfverfahrens sind lineare Fehler erlaubt, wie in Tabelle 19 angegeben.
Scheibengröße Anzahl der erlaubten Fehler mit ≥ 30 mm Länge
Tab. 19: Zulässige lineare Fehler in der Sichtfläche
Lineare Fehler von weniger als 30 mm Länge sind erlaubt.
8.5.5 Fehler in der Kantenfläche bei gerahmten Rändern
Nach dem unter 8.5.9 angegebenen Prüfverfahren sind Fehler ≤ 5 mm Durchmesser auf der Kantenfläche zulässig.
Bei Scheiben ≤ 5 m2 beträgt die Breite der Kantenfläche 15 mm. Diese erhöht sich bei Scheiben > 5m um 20 mm. Blasen dürfen nur auf bis zu 5 % der Kantenfläche vorkommen.
8.5.6 Kerben
Kerben sind nicht zulässig
8.5.7 Falten und Streifen
Falten und Streifen sind in der Sichtfläche nicht zulässig.
8.5.8 Fehler an Kanten, die nicht gerahmt werden
Verbundglas wird normalerweise in Rahmen eingebaut. Ist es ausnahmsweise ungerahmt, dürfen Kanten nur geschliffen, poliert oder als Gehrungskanten nach EN ISO12543-5 ausgeführt werden.
Unter diesen Bedingungen sind Ausmuschelungen, Blasen, Einziehungen und Fehler in der Zwischenschicht zulässig, wenn sie beid er Prüfung (s. 8.5.9) nicht sichtbar sind.
Für eine bestmögliche Kanten-Qualität sind Sichtkanten bei Bestellung vorzugeben. Die produktionsbedingte Abstellkante sowie Folienreste im Saumbereich bleiben jedoch erkennbar. Ist keine Sichtkante vorgegeben, sind Folienrückstände an den Kanten erlaubt.
8.5.9 Prüfverfahren
Das Verbundglas wird bei diffusem Tageslicht oder vergleichbarem Licht senkrecht vor und parallel zu einem matt-grauen Hintergrund aufgestellt. Der Betrachtungsabstand beträgt 2 m, der Betrachtungswinkel 90°. Störende Fehler bei dieser Betrachtungsweise müssen gekennzeichnet werden. Anschließend erfolgt die Beurteilung nach Spezifikation.
Allgemein:
Bei Außenverglasungen mit freier Bewitterung der Glaskanten kann sich durch die hygroskopische Eigenschaft der PVB-Folie in der Randzone der Farbeindruck je nach Umgebungsbedingungen verändern. Dies ist zulässig.
8.5.10 Farbfolien
Farbfolien und matte Folien verlieren durch Witterungseinflüsse an Farbintensität (z. B. UV-Strahlen).
Deshalb können bei Glasnachlieferungen mehr oder weniger sichtbare Farbunterschiede zu bereits eingebauten Gläsern des gleichen Typs auftreten. Dies ist kein Reklamationsgrund.
Bei Nachlieferungen können chargenbedingte Farbunterschiede auftreten.
8.5.11 VSG mit Stufen
Im Regelfall werden bei allen VSG-Gläsern mit Stufe Folien-Überstände im Stufenbereich abgeschnitten. Bei 2-scheibigen VSG-Elementen ist dies generell durchführbar und zu vereinbaren.
Bei 3- oder mehrscheibigen VSG-Gläsern, bei denen die mittlere(n) Scheibe(n) zu den äußeren Gläsern zurückversetzt ist(sind), wird die Folie abgeschnitten, wenn die Stufenbreite = Glasstärke der Mittelscheibe bzw. die Stufentiefe = den Glasdicken der Mittelscheiben ist.
Bei allen anderen Stufengrößen muss der Folien-Rückschnitt vereinbart werden.
Wenn die Entfernung der Folie wie beschrieben machbar ist, sind produktionstechnisch nicht gänzlich vermeidbare Rückstände kein Reklamationsgrund.
Bei allen anderen Stufen sind Folienreste bei den Stufen nicht entfernbar, dies ist ebenfalls kein Reklamationsgrund.
Der Kunde sollte die Abmessungen eines Gegenstücks, das in das VSG-Element geschoben wird, angeben.
Produktionsbedingte Folienrückstände an den Glaskanten können an der Abstellkante durch Auflagepunkte deformiert sein und sind kein Reklamationsgrund.
Abb. 17
8.5.12 Stempel
Eine nicht deckungsgleiche Lage der Stempel an den Einzelscheiben ist produktionstechnisch möglich.

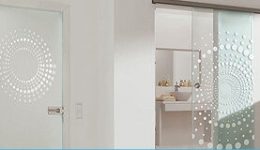
Ganzglastüren in Standardgrößen oder maßgefertigt. Entdecke hochwertige Glastüren für jede Wohnsituation
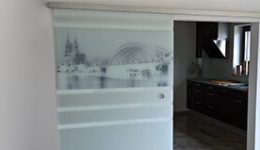
Hochwertige Glasschiebetüren in Standardgrößen oder als Anfertigung nach Maß passende für jeden Raum.
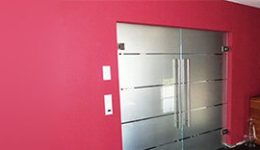
Schwingtüren aus Glas für Küche, Wohnzimmer oder Bad bringen ein individuelles Element in jede Wohnung.
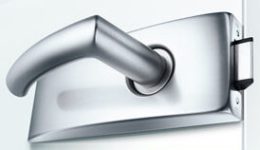
Beschläge für Glastüren als Einzelteil oder im Set von allen führendenden Markenherstellern.
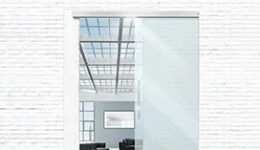
Vielfältige und Individuelle Schiebetürbeschläge für Glasschiebetüren oder Holzschiebtüren.
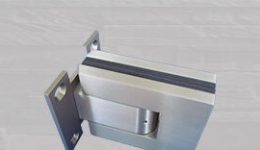
Pendeltürbeschläge für alle gängigen Pendeltüren als einzelteil oder im Set.
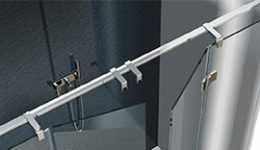
Glasduschen für Nischen. Individuell gestalten und einbauen.